The chemical processing plant is one of the most popular manufacturing industries in the world. It is vital in producing many products, including fuels, fertilizers, medicines, and plastics. However, we know that chemicals are usually harmful to the human body. Therefore, ensuring safety is the prime concern in these industries. Weatherstripping, in this case, is a crucial component that makes the operation safe and efficient.
High-quality seal strips or weatherstripping are used to prevent the leakage of chemicals. It protects the manufacturing equipment from damage and corrosion. In addition, it ensures the flow of chemicals through the equipment is effective and efficient. Therefore, selecting a suitable weatherstripping material is very crucial. It would be best if you considered it to ensure the integrity of the chemical equipment.
On the other hand, different weatherstripping materials offer varying mechanical properties. These properties include temperature resistance, chemical resistance, and abrasion resistance levels. In this case, depending on the type of chemicals processing in the production, you should choose the suitable seal strip material. It is important to note that selecting the suitable seal strip material is very important. And you must do it to protect the equipment and improve the overall performance of the production.
However, this article highlights the importance of seal strips in chemical processing. In addition, it will also determine the varying types of seal strips available for chemical processing equipment. It will also discuss the most common types of seal strip materials and the critical factors of choosing a suitable material.
How Weatherstripping Works Against Chemicals
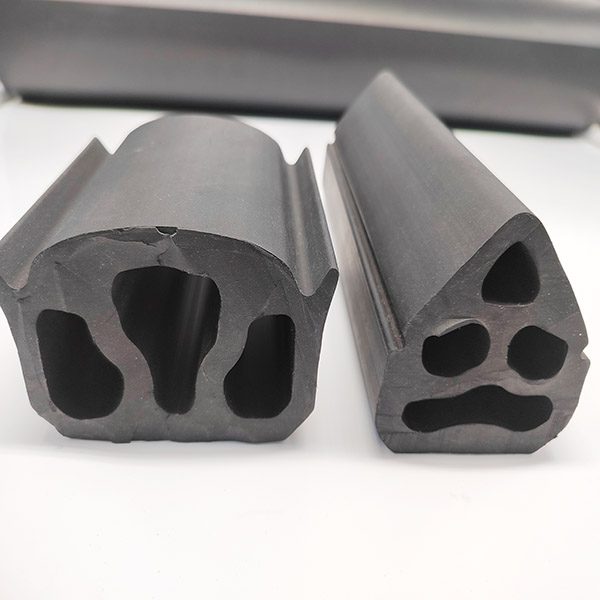
Chemical-resistant weatherstrippings create a barrier between the chemical and the machinery. As a result, these chemicals can not leak through, which may cause equipment corrosion. However, the effectiveness of this barrier depends on the type of seal strip material used. We know that different seal strip materials offer varying chemical resistance properties.
EPDM is a perfect example of a weatherstripping material that resists various chemicals. These chemicals might include acids, bases, or polar solvents. On the other hand, silicone seal strip is another ideal material with high chemical resistance ability. Neoprene is also one of the most popular synthetic rubber that works perfectly against oils, solvents, and fuels. Although, this material may not be suitable for harsher chemicals.
Seal strips or weatherstrippings help prevent the chemical from infiltrating the equipment. Therefore, choosing the suitable seal strip material and ensuring proper installation is necessary. Finally, your equipment can be protected from the damaging effects of chemicals.
Applications of Weatherstrippings in The Chemical Industry
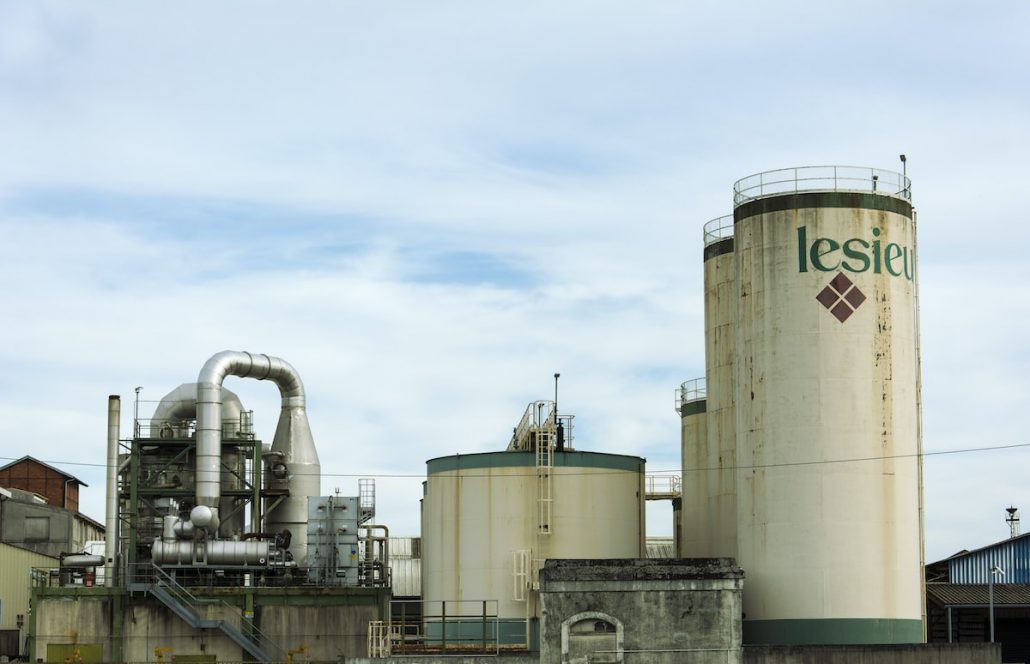
Sealing strips are a barrier between the chemical and the machinery used in chemical processing. Therefore, it has many applications used in this manufacturing process. Following are the six most popular applications of seal strips seen in chemical industries.
- Storage tanks: Seal strips prevent the leakage of chemicals from the large chemical storage tanks. This type of weatherstripping typically protects the chemical tanks from corrosion.
- Chemical processing vessels: Vessels in chemical processing have two types. They include with and without internals. However, seal strips typically seal the openings in these process vessels. It prevents the leakage of chemicals and protects from corrosion.
- Transfer lines: Seal strips are popular in sealing the connection between the large transfer lines. Hoses and pipes are excellent examples of these applications. This weatherstripping usually prevents the chemical from leakage during transfer.
- Reactors and distillation columns: Seal strips seal the openings in chemical reactors. It may also be seen in distillation columns to prevent the chemical from coming outside.
- Valves and flowmeters: Seal strips seal the openings in chemical reactors. It may also be seen in distillation columns to prevent the chemical from coming outside.
- Chemical Storage Vehicles: Storage vehicles such as trailers require various seal strips. They protect the chemical from harsh environments.
Seal strips are popular in chemical industries for their excellent mechanical properties. These properties include chemical resistance, temperature resistance, and abrasion resistance properties.
Benefits of Using Weatherstripping in Chemical Processing
Seal strips provide high temperature and chemical resistance properties. So, they provide considerable benefits in chemical manufacturing. The following are the most crucial benefits in chemical industries.
- Safety: Seal strips prevent leakage of chemicals that may harm both environment and workers. In this situation, seal strips ensure a safe working environment for the workers in the production line.
- Increased equipment lifespan: Seal strips protect equipment from corrosion and damage. As a result, these seal strips offer an increased lifespan to this chemical machinery.
- Low maintenance cost: Seal strips protect the equipment from corrosion and damage caused by the chemicals. So, it ultimately saves the repair cost. On the other hand, this equipment requires less maintenance since seal strips provide an increased lifespan.
- Improved efficiency: High-quality seal strips or weatherstripping ensures effective and efficient manufacturing.
- Controlled emission: High-quality EPDM seal strips prevent chemicals and emissions. As a result, it improves the overall environmental impact of the chemical facility.
- Reliability: Seal strips ensure a safe working environment. So, it creates reliability among the workers. Accordingly, workers can confidently handle all the jobs.
How to Choose The Suitable Seal Strips for Chemical Works
Seal strips play a vital role in chemical processing. It is an essential part of every equipment used in chemical manufacturing. So, choosing suitable seal strips or weatherstripping is crucial. While selecting the seal strips, there are several factors that you should consider. Some of these factors are:
- Chemical compatibility: First, you should ensure the compatibility of the seal strips with the chemical used. The incompatible seal strips may degrade or become brittle leading to unexpected failures.
- Temperature resistance: The chosen seal strips must withstand the given temperature. Some seal strips are ideal for high-temperature applications, while others are not.
- Abrasion resistance: It is a critical factor that controls the friction or movement of the system. Seal strips of large pump shafts require high-quality abrasion resistance properties. It is necessary for withstanding high-frictional force produced by the system.
- Pressure resistance is one of the most critical factors you should consider. Chemical processing deals with varying pressures. As a result, the seal strip used in the equipment must withstand certain pressure levels.
- Size and dimension: You should check the appropriate size and shape of the seal strips that fit the equipment.
- Compliance: The seal strip you choose must comply with any regulatory requirements.
Above all, remember to collect all the necessary documents which elaborate on the above factors. okin Rubber provides authentic and tested papers from the lab. So, consider the above factors before choosing suitable seal strips or weatherstripping. Considering these factors, your chemical processing equipment can perform better.
Popular Weatherstripping From okin Rubber For Chemical Processing
In this section, we will talk about the most popular seal strip materials that you may choose from okin rubber. You can select the following materials depending on your suitable application and budget. However, okin rubber is a leading supplier of industrial rubber products. Their products also include seal strips for chemical processing.
- EPDM Seal strips: EPDM is a synthetic rubber excellent for durability and chemical and weather resistance. These seal strips material is popular in various chemical processing applications.
- Silicone seal strips: It is famous for resistance to high temperatures and harsh environments. Silicone seal strips are prevalent in high-temperature or extreme conditions.
- Neoprene seal strips are famous for their excellent resistance to oils, solvents, and fuels. Neoprene seal strips are prevalent in chemical applications involving exposure to these chemicals. Although, this type of seal strip may not be suitable for harsher environments.
- Viton seal strips are a type of fluoroelastomers. They are famous for their excellent chemical and high-temperature resistance.
- PTFE seal strips: PTDE is especially famous for its excellent non-stick properties. Besides, they are also good at chemical resistance, high temperature, and non-stick properties.
Case Study: Seal Strips in Petrochemical Industry
Successful implementation of seal strips is in a giant petrochemical facility. In this facility, frequent leaks and equipment failures are the primary considerations. After consecutive research, this facility decided to replace its existing seal strips with EPDM.
EPDM is a synthetic rubber famous for its chemical, weather, and high-temperature resistance. This weatherstripping material prevents chemicals from leaking and sweeping. It protects the equipment used in the process and provides a long-lasting lifespan. Above all, EPDM is the best choice for any sealing application.
Summary
Seal strips play a significant role in preserving the integrity of machinery used in chemical processing plants. They create a barrier that prevents chemicals from leaking or sweeping. As a result, it protects the chemical processing equipment from damage and corrosion. Therefore, choosing a suitable weatherstripping material for chemical processing applications is crucial.
While choosing the suitable seal strip material, we must consider the abovementioned factors. You can also choose from varying types of seal strip materials. But EPDM seal strips are considered the best materials in most typical applications.
Above all, if you still have questions regarding today’s article, don’t hesitate to contact our customer service team. You would be happy to hear that okin rubber keeps the best customer service team for their customer.